Navigating the Shop Floor with Confidence: A Comprehensive Guide to Automatic Collision Avoidance (ACA) Systems
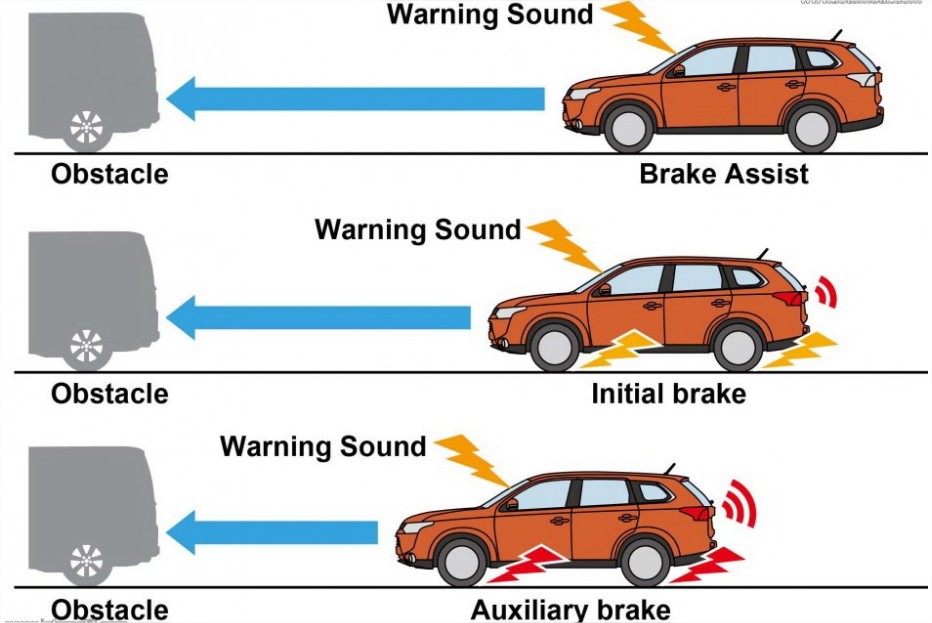
In the dynamic world of CNC machining, ensuring the safety of operators, machines, and tools is paramount. Automatic Collision Avoidance (ACA) systems have emerged as a game-changer, providing an extra layer of protection against accidental collisions during machining operations. This comprehensive guide delves into the intricacies of ACA systems, empowering you to leverage their capabilities for a safer and more efficient machining environment.
Unveiling the Technology: How ACA Systems Work
ACA systems rely on a combination of sensors, software algorithms, and the CNC control unit to prevent collisions between various elements within the machine workspace. Here’s a breakdown of the key components:
Sensors: The eyes and ears of the ACA system, these sensors perceive the environment surrounding the cutting tool and other machine components. Common sensors include:
- Proximity sensors: Detect the presence of nearby objects without physical contact.
- Laser scanners: Create a detailed 3D map of the workspace using laser beams.
- Encoders: Track the position and movement of the machine axes.
- Vision systems: Utilize cameras to visually identify objects within the workspace.
Software Algorithms: The brain of the ACA system, these algorithms process sensor data in real-time. They compare the actual position of the tool and other machine components with the programmed toolpath and pre-defined safety zones. If a potential collision is detected, the algorithms trigger corrective actions.
CNC Control Unit: The central nervous system of the machine, the CNC control unit receives signals from the ACA system and translates them into actionable commands. These commands might involve stopping or slowing down the machine axes, issuing warnings to the operator, or activating other safety protocols.
Types of Automatic Collision Avoidance Systems: Understanding the Options
ACA systems come in various forms, each offering a different level of protection and functionality:
Basic Collision Detection Systems: These entry-level systems primarily utilize proximity sensors to detect potential collisions between the tool and the machine structure or fixturing. Upon detecting a potential collision, the system might trigger an alarm or halt machine movement altogether.
Software-Based Collision Prediction: These more advanced systems leverage the programmed toolpath data and the machine’s kinematic model to predict potential collisions before they occur. This allows for preventive measures like slowing down tool movement or issuing warnings to the operator.
Sensor-Based Collision Avoidance Systems: These systems utilize a network of sensors (like laser scanners or vision systems) to create a real-time map of the workspace. This allows for more comprehensive collision detection, not just with the machine structure but also with any objects inadvertently placed within the workspace.
Adaptive Collision Avoidance Systems: The pinnacle of ACA technology, these systems integrate real-time sensor data with advanced algorithms to dynamically adjust the toolpath during machining. This allows for automatic collision avoidance even in unforeseen situations, such as tool deflection or workpiece movement.
By understanding the different types of ACA systems available, you can select the one that best suits your specific needs and machining environment.
Utilizing ACA Systems Effectively: Best Practices for Implementation
To maximize the benefits of ACA systems, here are some crucial best practices to consider:
Proper System Setup and Calibration: Ensure the ACA system is correctly installed and calibrated according to the manufacturer’s instructions. This involves defining safety zones, setting sensor sensitivity levels, and verifying the system’s functionality through test runs.
Maintaining a Clean Work Envelope: A cluttered workspace with stray tools or materials can confuse the ACA system’s sensors and lead to false positives. Maintaining a clean and organized work envelope is essential for reliable ACA system operation.
Operator Awareness and Training: While ACA systems provide an extra layer of protection, they don’t eliminate the need for operator vigilance. Train operators on the capabilities and limitations of the ACA system and emphasize the importance of safe operating practices.
Regular System Checks and Maintenance: Like any machine component, ACA systems require periodic checks and maintenance. This might involve cleaning sensors, verifying system performance through test runs, and updating software if necessary.
By adhering to these best practices, you can ensure your ACA system functions optimally, safeguarding your machine tools, operators, and overall machining environment.
The Future of ACA Systems: Embracing Continuous Improvement
As technology advances, ACA systems are poised to become even more sophisticated and ubiquitous in the world of CNC machining. Here’s a glimpse into what the future holds:
Enhanced Sensor Integration: The incorporation of new sensor technologies, such as 3D cameras and force sensors, can provide even more comprehensive data about the machining environment, enabling more nuanced collision detection and avoidance strategies.
AI-Powered Collision Prediction: Artificial intelligence algorithms are being explored to analyze sensor data and predict potential collisions with even greater accuracy.
In the dynamic world of CNC machining, ensuring the safety of operators, machines, and tools is paramount. Automatic Collision Avoidance (ACA) systems have emerged as a game-changer, providing an extra layer of protection against accidental collisions during machining operations. This comprehensive guide delves into the intricacies of ACA systems, empowering you to leverage their capabilities for a safer and more efficient machining environment.
Unveiling the Technology: How ACA Systems Work
ACA systems rely on a combination of sensors, software algorithms, and the CNC control unit to prevent collisions between various elements within the machine workspace. Here’s a breakdown of the key components:
Sensors: The eyes and ears of the ACA system, these sensors perceive the environment surrounding the cutting tool and other machine components. Common sensors include:
- Proximity sensors: Detect the presence of nearby objects without physical contact.
- Laser scanners: Create a detailed 3D map of the workspace using laser beams.
- Encoders: Track the position and movement of the machine axes.
- Vision systems: Utilize cameras to visually identify objects within the workspace.
Software Algorithms: The brain of the ACA system, these algorithms process sensor data in real-time. They compare the actual position of the tool and other machine components with the programmed toolpath and pre-defined safety zones. If a potential collision is detected, the algorithms trigger corrective actions.
CNC Control Unit: The central nervous system of the machine, the CNC control unit receives signals from the ACA system and translates them into actionable commands. These commands might involve stopping or slowing down the machine axes, issuing warnings to the operator, or activating other safety protocols.
Types of Automatic Collision Avoidance Systems: Understanding the Options
ACA systems come in various forms, each offering a different level of protection and functionality:
Basic Collision Detection Systems: These entry-level systems primarily utilize proximity sensors to detect potential collisions between the tool and the machine structure or fixturing. Upon detecting a potential collision, the system might trigger an alarm or halt machine movement altogether.
Software-Based Collision Prediction: These more advanced systems leverage the programmed toolpath data and the machine’s kinematic model to predict potential collisions before they occur. This allows for preventive measures like slowing down tool movement or issuing warnings to the operator.
Sensor-Based Collision Avoidance Systems: These systems utilize a network of sensors (like laser scanners or vision systems) to create a real-time map of the workspace. This allows for more comprehensive collision detection, not just with the machine structure but also with any objects inadvertently placed within the workspace.
Adaptive Collision Avoidance Systems: The pinnacle of ACA technology, these systems integrate real-time sensor data with advanced algorithms to dynamically adjust the toolpath during machining. This allows for automatic collision avoidance even in unforeseen situations, such as tool deflection or workpiece movement.
By understanding the different types of ACA systems available, you can select the one that best suits your specific needs and machining environment.
Utilizing ACA Systems Effectively: Best Practices for Implementation
To maximize the benefits of ACA systems, here are some crucial best practices to consider:
Proper System Setup and Calibration: Ensure the ACA system is correctly installed and calibrated according to the manufacturer’s instructions. This involves defining safety zones, setting sensor sensitivity levels, and verifying the system’s functionality through test runs.
Maintaining a Clean Work Envelope: A cluttered workspace with stray tools or materials can confuse the ACA system’s sensors and lead to false positives. Maintaining a clean and organized work envelope is essential for reliable ACA system operation.
Operator Awareness and Training: While ACA systems provide an extra layer of protection, they don’t eliminate the need for operator vigilance. Train operators on the capabilities and limitations of the ACA system and emphasize the importance of safe operating practices.
Regular System Checks and Maintenance: Like any machine component, ACA systems require periodic checks and maintenance. This might involve cleaning sensors, verifying system performance through test runs, and updating software if necessary.
By adhering to these best practices, you can ensure your ACA system functions optimally, safeguarding your machine tools, operators, and overall machining environment.
The Future of ACA Systems: Embracing Continuous Improvement
As technology advances, ACA systems are poised to become even more sophisticated and ubiquitous in the world of CNC machining. Here’s a glimpse into what the future holds:
Enhanced Sensor Integration: The incorporation of new sensor technologies, such as 3D cameras and force sensors, can provide even more comprehensive data about the machining environment, enabling more nuanced collision detection and avoidance strategies.
AI-Powered Collision Prediction: Artificial intelligence algorithms are being explored to analyze sensor data and predict potential collisions with even greater