PowerMill Ultimate: Unleashing the Potential of Cutting Tools
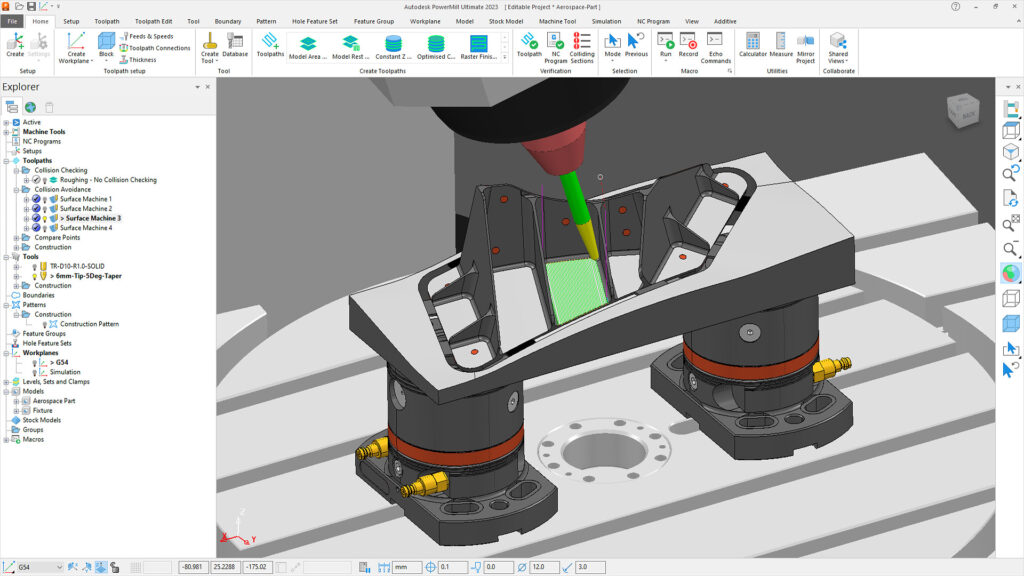
PowerMill Ultimate empowers you to leverage a vast array of cutting tools to tackle diverse machining applications. This comprehensive guide delves into the world of PowerMill cutting tools, equipping you with the knowledge to select the right tool for the job and maximize machining efficiency.
Understanding the Cutting Tool Arsenal: A Classification Primer
PowerMill offers a comprehensive library of cutting tools categorized based on their geometry, application, and material suitability. Here’s a breakdown of some key cutting tool classifications:
End Mills: These versatile workhorses are characterized by a shank and flutes that spiral around a cutting edge. Common end mill types include:
- Ball nose end mills: Ideal for creating curved surfaces and profiles.
- Flat end mills: Used for generating flat surfaces, pockets, and slots.
- Bull nose end mills: Offer a combination of flat and curved cutting edges for creating radii and transitions.
- Corner rounding end mills: Specifically designed for rounding corners and edges.
Ball Nose Cutters: These feature a spherical cutting edge ideal for creating smooth, contoured surfaces and hemispherical features.
Face Mills: Designed for machining large, flat surfaces efficiently. They feature multiple cutting inserts positioned around a central body.
Drills and Boring Tools: These create cylindrical holes in workpieces. Common types include:
- Twist drills: General-purpose drills with a helical flute for chip evacuation.
- Center drills: Used to create pilot holes for larger diameter drills.
- Boring bars: Long, slender tools with a single cutting insert for high-precision deep hole drilling.
Turning Tools: While PowerMill isn’t primarily a turning software, it can accommodate turning toolpaths for integrated mill-turn operations. Common turning tools include:
- Cutting inserts: Replaceable cutting edges with various geometries for different machining tasks.
- Tool holders: Securely grip the cutting inserts and provide an interface with the machine tool.
Specialty Tools: PowerMill also supports an array of specialized cutting tools for specific applications, such as thread milling tools, gear cutting tools, and form tools for creating specific profiles.
By understanding these core cutting tool classifications and their functionalities, you can make informed decisions when selecting the appropriate tool for your machining needs.
Selecting the Right Tool for the Job: Factors to Consider
Choosing the optimal cutting tool for a specific machining operation requires careful consideration of various factors:
Workpiece Material: Different materials require cutting tools with specific properties. For instance, machining hard steels might necessitate carbide tools, while softer materials like aluminum might be machined with high-speed steel (HSS) tools.
Feature Geometry: The geometry of the feature being machined dictates the type of cutting tool best suited for the job. For instance, creating a pocket requires a flat end mill, while machining a curved surface might necessitate a ball nose end mill.
Desired Surface Finish: The desired surface finish of the machined feature influences the choice of cutting tool. Fine-finishing operations might require smaller diameter tools with higher cutting edge sharpness, while roughing operations can utilize larger diameter tools with higher feed rates.
Machining Efficiency: Factors like tool material, geometry, and coating can impact machining efficiency. Selecting tools that optimize factors like chip removal, tool life, and cutting speeds can significantly improve overall machining productivity.
Machine Capabilities: Consider the specifications of your CNC machine, such as spindle power and maximum tool diameter, when selecting cutting tools. Utilizing tools exceeding the machine’s capabilities can lead to tool breakage or machine damage.
PowerMill Toolpath Strategies: Optimizing Tool Usage
PowerMill offers various toolpath strategies that leverage the capabilities of different cutting tools effectively:
2D Contour Milling: This strategy utilizes end mills to follow a 2D profile, ideal for machining pockets, slots, and contours.
3D Roughing and Finishing: These strategies employ various toolpaths with different cutting parameters to remove material efficiently for roughing and achieve a desired surface finish for finishing.
Hole Making: PowerMill offers specific toolpath strategies for drilling, reaming, tapping, and boring operations, optimizing tool usage for these applications.
Multi-Axis Machining: For complex 3D geometries, PowerMill generates toolpaths that utilize multiple machine axes and specialized cutting tools, such as ball nose end mills or 5-axis tooling.
By mastering these toolpath strategies and understanding their interaction with different cutting tools, you can unlock the full potential of PowerMill for efficient and precise machining.