Mastering Precision and Efficiency: An In-depth Exploration of Sheet Metal Design in SolidWorks
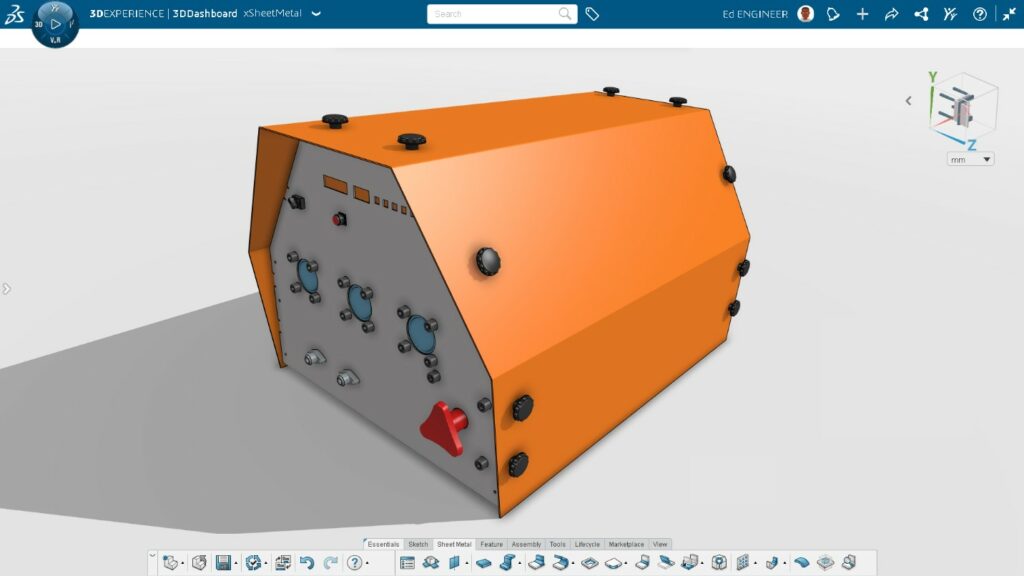
Sheet metal design stands as a fundamental aspect within SolidWorks, offering designers and engineers a versatile toolset to create intricate sheet metal components with precision and efficiency. In this exhaustive guide, we delve into the intricacies of sheet metal design in SolidWorks, unraveling its functionality, benefits, and practical applications across various design and engineering disciplines.
Understanding Sheet Metal Design:
Sheet metal design in SolidWorks involves the creation and manipulation of thin-walled components made from flat sheet materials, such as steel, aluminum, or copper. These components may include enclosures, brackets, panels, housings, and other structures commonly found in various industries, including automotive, aerospace, electronics, and manufacturing.
At the core of sheet metal design lies the concept of specialized sheet metal features and tools, which enable users to model and unfold sheet metal parts accurately while considering factors such as bend allowance, bend relief, and material thickness. These features streamline the design process and ensure that sheet metal components can be manufactured efficiently and cost-effectively.
Key Concepts of Sheet Metal Design in SolidWorks:
- Sheet Metal Features: SolidWorks provides a range of dedicated sheet metal features and tools tailored to the unique requirements of sheet metal design. These features include base flanges, edge flanges, bends, hems, ribs, and louvers, each designed to facilitate the creation of specific sheet metal geometries and configurations.
- Sheet Metal Parameters: Sheet metal design in SolidWorks involves defining and managing parameters that govern the behavior and geometry of sheet metal components. These parameters include material thickness, bend radius, bend angle, K-factor, and relief types, which determine how sheet metal parts are formed, bent, and assembled.
- Unfolding and Folding: SolidWorks allows users to unfold and fold sheet metal parts seamlessly, enabling them to transition between flattened and formed states effortlessly. Unfolding converts formed sheet metal parts into flat patterns, facilitating manufacturing and fabrication processes, while folding restores flat patterns to their original 3D shapes, allowing designers to visualize and manipulate components in their assembled state.
- Design Considerations: Sheet metal design in SolidWorks requires careful consideration of manufacturing constraints and design guidelines to ensure that components can be produced accurately and efficiently. Factors such as bend radius, bend allowance, minimum flange length, and hole-to-edge distance influence the manufacturability and quality of sheet metal parts and must be accounted for during the design process.
Benefits of Sheet Metal Design in SolidWorks:
- Design for Manufacturability: Sheet metal design in SolidWorks enables designers to create components optimized for manufacturing processes such as bending, punching, cutting, and forming. By incorporating manufacturability considerations early in the design process, designers can minimize production costs, reduce lead times, and improve product quality and consistency.
- Accuracy and Precision: Sheet metal design in SolidWorks ensures high levels of accuracy and precision in sheet metal components, as features and dimensions are defined parametrically and maintained dynamically. This accuracy extends to manufacturing processes, where precise geometric data is essential for achieving tight tolerances and ensuring proper fit and function of sheet metal parts.
- Efficiency and Productivity: Sheet metal design in SolidWorks streamlines the design process and enhances productivity by providing a dedicated set of tools and features tailored to sheet metal design tasks. Designers can create sheet metal components rapidly, iterate on design concepts efficiently, and generate accurate flat patterns and manufacturing drawings automatically, reducing time-to-market and enhancing competitiveness.
- Design Optimization: Sheet metal design in SolidWorks enables designers to optimize sheet metal components for performance, cost, and manufacturability. By exploring different design configurations, material choices, and manufacturing methods, designers can identify and implement design improvements that enhance functionality, durability, and efficiency while minimizing production costs and waste.
Practical Applications of Sheet Metal Design in SolidWorks:
- Enclosures and Cabinets: Sheet metal design is commonly used for creating enclosures, cabinets, and housings for electronic devices, machinery, and equipment. Designers leverage sheet metal features and tools to model complex enclosure geometries, incorporate mounting features and access openings, and optimize designs for ventilation, heat dissipation, and cable management.
- Structural Components: Sheet metal design is employed in the creation of structural components such as brackets, supports, frames, and chassis for various applications. Designers use sheet metal features to model lightweight, yet robust structures that withstand loads, vibrations, and environmental conditions while minimizing material usage and weight.
- Automotive Panels and Body Components: Sheet metal design plays a critical role in automotive design and manufacturing, where sheet metal components form the basis of vehicle panels, body structures, and interior trim. Designers use sheet metal features to model complex automotive geometries, such as fenders, doors, hoods, and trunk lids, optimizing designs for aerodynamics, safety, and aesthetics.
- Sheet Metal Fabrication: Sheet metal design supports the fabrication of sheet metal parts through processes such as cutting, bending, welding, and stamping. Manufacturers leverage sheet metal flat patterns generated from SolidWorks models to produce accurate templates for cutting and forming sheet metal parts, ensuring precision and consistency in manufacturing operations.
Conclusion:
Sheet metal design in SolidWorks is a versatile and indispensable tool that empowers designers and engineers to create intricate sheet metal components with precision and efficiency. By leveraging specialized features, parameters, and tools tailored to sheet metal design tasks, designers can streamline the design process, optimize designs for manufacturability, and produce high-quality sheet metal parts that meet stringent requirements and specifications. Whether used for product enclosures, structural components, automotive panels, or sheet metal fabrication, sheet metal design in SolidWorks remains a cornerstone of modern engineering workflows, enabling users to master complexity and achieve excellence in their designs.