PowerMill Ultimate: Sculpting the Path to Perfection – A Comprehensive Guide to Editing Toolpath Parameters
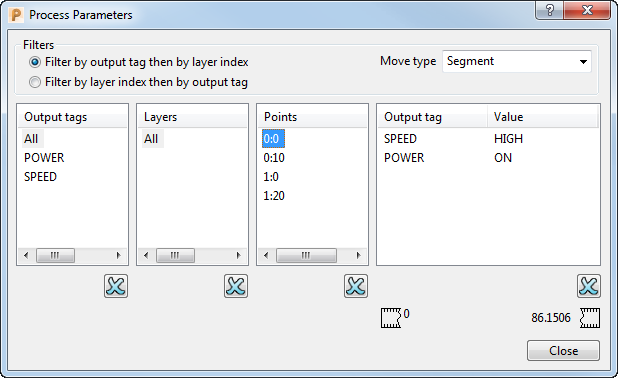
PowerMill Ultimate empowers you to not only generate sophisticated toolpaths but also to meticulously edit and refine them. This meticulous control over toolpath parameters allows for fine-tuning machining strategies, optimizing cutting efficiency, and ultimately achieving parts with exceptional quality and precision. This comprehensive guide delves into the world of toolpath editing in PowerMill Ultimate, equipping you with the knowledge and techniques to sculpt the perfect path for your machining endeavors.
Understanding the Building Blocks: Essential Toolpath Parameters
Before delving into editing techniques, it’s crucial to understand the core toolpath parameters that govern the movement of the cutting tool:
Toolpath Geometry: This defines the path the tool center point (TCP) will follow during machining. It can be a simple line, a complex curve, or a freeform surface depending on the machining operation.
Cutting Conditions: These parameters specify how aggressively the tool removes material, including:
- Spindle Speed (RPM): The rotational speed of the cutting tool.
- Feed Rate (mm/min or in/min): The speed at which the tool moves along the toolpath.
- Chip Load (mm/tooth or in/tooth): The thickness of the chip removed by the tool with each revolution.
Approach and Retract Strategies: These define how the tool enters and exits the material during machining, impacting factors like surface finish and tool wear.
Coolant Settings: Specify the type and flow rate of coolant used during machining, which is crucial for chip evacuation, temperature control, and tool life.
By understanding these fundamental parameters, you can approach toolpath editing with a clear understanding of how adjustments will influence the machining process.
Editing Techniques Exposed: A Pro’s Toolkit
PowerMill Ultimate offers a comprehensive suite of functionalities for editing toolpath parameters. Here’s a breakdown of some key techniques to master:
Global Parameter Editing: This allows you to modify parameters for the entire toolpath simultaneously. For instance, you can adjust spindle speed across the entire toolpath to achieve a more consistent cutting force.
Segment-Specific Editing: PowerMill allows for editing parameters for individual segments within a toolpath. This is useful for localized adjustments, such as reducing feed rate in tight corners to minimize tool deflection or increasing chip load in open areas for faster material removal.
Toolpath Recalculation: After modifying parameters, recalculating the toolpath ensures the tool movement reflects the changes you’ve made. PowerMill offers various recalculation options, allowing you to selectively update specific portions of the toolpath or regenerate the entire path based on the new parameters.
Advanced Editing Techniques: PowerMill provides advanced editing functionalities for experienced users. These include:
- Offsetting the Toolpath: Moving the toolpath a specific distance in a chosen direction. This can be useful for machining multiple features with a single toolpath by offsetting it for each feature.
- Trimming and Extending Toolpaths: Modifying the start and end points of the toolpath to adjust its machining area.
- Splitting and Merging Toolpaths: Dividing a single toolpath into multiple segments or combining separate toolpaths for efficient machining sequences.
By mastering these editing techniques, you gain the ability to manipulate toolpaths with precision, tailoring them to achieve optimal machining performance for your specific needs.
Editing Strategies for Efficiency: Optimizing Your Approach
Here are some practical strategies to consider when editing toolpath parameters:
Start with Roughing Operations: Focus your initial editing efforts on roughing toolpaths, where aggressive material removal is the primary goal. Optimizing cutting conditions in roughing can significantly reduce overall machining time.
Prioritize Surface Finish in Finishing Operations: When editing finishing toolpaths, prioritize parameters that influence surface finish, such as feed rate and step-over (the distance between adjacent tool passes).
Balance Cutting Efficiency with Tool Life: While aggressive cutting conditions can expedite machining, consider the impact on tool wear. Editing parameters to find the optimal balance between efficiency and tool life is crucial for long-term cost-effectiveness.
Leverage Simulation Tools: PowerMill’s simulation capabilities allow you to visualize the edited toolpath and assess potential issues like collisions or gouging before executing the actual machining process. This helps refine your edits and minimize the risk of errors.
By following these strategies, you can transform toolpath editing from a remedial task to a powerful optimization tool, ensuring your machining processes achieve the desired balance of efficiency, precision, and cost-effectiveness.