Mastering Heat Transfer Simulation in ANSYS Fluent: A Comprehensive Guide
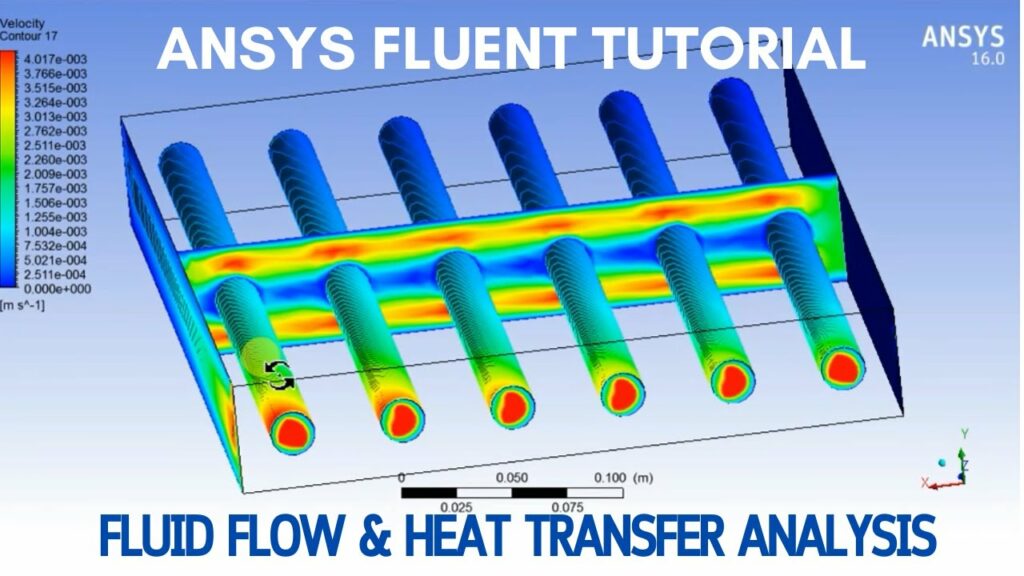
Introduction: Heat transfer simulation plays a crucial role in engineering design and analysis, allowing engineers to predict and optimize the thermal behavior of systems and components. ANSYS Fluent is a powerful computational fluid dynamics (CFD) software tool widely used for simulating heat transfer phenomena in complex geometries and fluid flow environments. In this comprehensive guide, we will explore the intricacies of simulating heat transfer in ANSYS Fluent, covering everything from model setup to results interpretation and optimization.
Section 1: Understanding Heat Transfer Phenomena 1.1 Introduction to Heat Transfer: Heat transfer is the process by which thermal energy is exchanged between different regions of a system or between a system and its surroundings. Three main mechanisms of heat transfer include conduction, convection, and radiation. Conduction involves the transfer of heat through a solid material, convection involves the transfer of heat through a fluid medium, and radiation involves the transfer of heat through electromagnetic waves.
1.2 Applications of Heat Transfer Simulation: Heat transfer simulation finds applications across various industries, including aerospace, automotive, electronics cooling, and HVAC systems. Engineers use heat transfer simulation to analyze thermal management issues, optimize cooling strategies, and ensure the reliability and performance of components and systems operating under thermal loads. ANSYS Fluent provides advanced tools for simulating heat transfer phenomena and predicting temperature distributions in complex geometries.
Section 2: Setting Up Heat Transfer Models in ANSYS Fluent 2.1 Defining Geometry and Boundary Conditions: The first step in simulating heat transfer in ANSYS Fluent is to define the geometry of the system or component of interest. Engineers can import CAD models or create geometry directly within ANSYS DesignModeler. Once the geometry is defined, boundary conditions such as inlet and outlet temperatures, heat sources, and thermal properties of materials must be specified to set up the simulation properly.
2.2 Mesh Generation: Mesh generation plays a crucial role in the accuracy and efficiency of heat transfer simulations. Engineers must generate a high-quality mesh that resolves the geometry accurately and captures the thermal gradients within the domain. ANSYS Fluent offers a variety of meshing tools, including structured and unstructured meshing algorithms, to generate meshes of varying complexity. Engineers must ensure that the mesh is sufficiently refined near regions of interest, such as solid-fluid interfaces and areas of high thermal gradients.
Section 3: Choosing Heat Transfer Models and Solvers 3.1 Heat Transfer Models: ANSYS Fluent offers several heat transfer models to simulate different heat transfer mechanisms accurately. Engineers can choose from options such as steady-state or transient heat conduction, laminar or turbulent convection, and surface-to-surface radiation models. The selection of appropriate heat transfer models depends on the specific characteristics of the system and the phenomena being simulated.
3.2 Solver Settings: Engineers must configure solver settings to ensure accurate and efficient convergence of heat transfer simulations. ANSYS Fluent offers a variety of solver algorithms and solution methods for solving the governing equations of heat transfer, including pressure-based and density-based solvers. Engineers must specify convergence criteria, time-step sizes, and other solver settings to control the accuracy and stability of the simulation.
Section 4: Running Heat Transfer Simulations and Analyzing Results 4.1 Running Simulations: Once the model setup is complete, engineers can run heat transfer simulations in ANSYS Fluent. During simulation, ANSYS Fluent solves the governing equations of heat transfer, including the conservation of mass, momentum, and energy, to predict temperature distributions within the domain. Engineers can monitor the simulation progress and assess convergence to ensure that the results are reliable and accurate.
4.2 Analyzing Results: After simulation, engineers can analyze the results to gain insights into the thermal behavior of the system. ANSYS Fluent provides visualization tools to display temperature contours, heat flux distributions, and other relevant quantities. Engineers can examine temperature profiles, identify regions of heat accumulation or heat loss, and assess the effectiveness of cooling strategies. Additionally, engineers can extract quantitative data such as average temperatures, heat transfer rates, and thermal gradients for further analysis.
Section 5: Optimization and Design Validation 5.1 Design Optimization: Based on the analysis results, engineers can identify opportunities to optimize the thermal performance of the system. This may involve modifying geometry, adjusting boundary conditions, or optimizing material properties to enhance heat transfer efficiency and mitigate thermal issues. By iteratively refining the design and rerunning simulations in ANSYS Fluent, engineers can optimize the thermal performance of components and systems to meet design requirements.
5.2 Design Validation: Heat transfer simulation in ANSYS Fluent allows engineers to validate the thermal performance of designs and assess their compliance with design requirements and specifications. Engineers can compare simulation results with experimental data or analytical solutions to verify the accuracy of the simulations. By conducting thorough validation studies, engineers can ensure that the simulated results are reliable and can be used with confidence for engineering design and analysis.
Conclusion: Heat transfer simulation in ANSYS Fluent provides engineers with a powerful tool for predicting and optimizing the thermal behavior of systems and components. By mastering the techniques outlined in this guide and leveraging the capabilities of ANSYS Fluent, engineers can simulate heat transfer phenomena accurately and efficiently, optimize designs for thermal performance, and develop innovative solutions to thermal management challenges. With practice, experimentation, and continuous learning, engineers can leverage the full potential of ANSYS Fluent to advance the field of heat transfer simulation and engineering design.