Mastering Heat Exchanger Modeling and Simulation in HTRI: A Comprehensive Guide
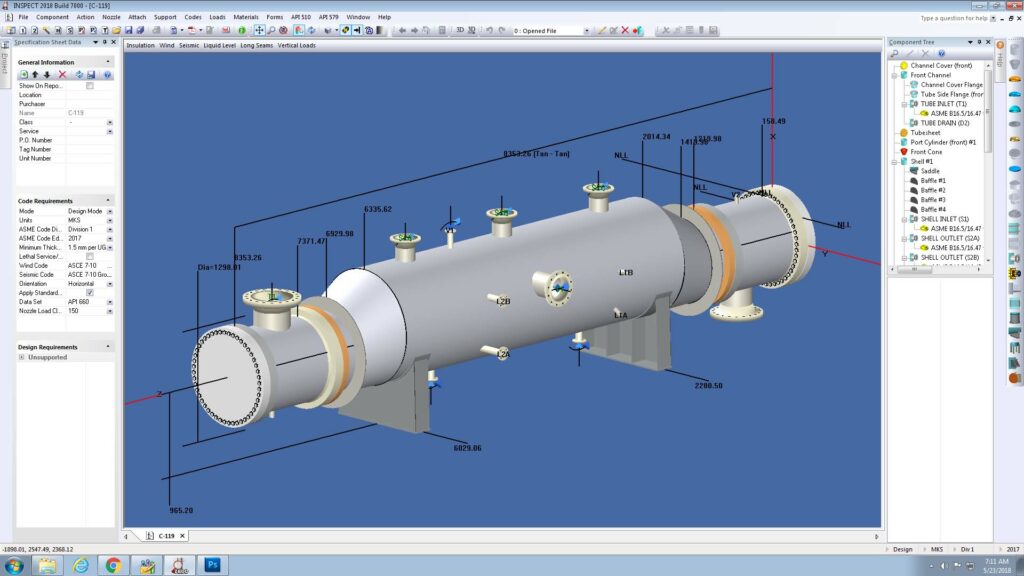
Introduction: Heat exchangers play a pivotal role in various industrial processes, facilitating the transfer of thermal energy between fluids to achieve heating, cooling, or condensation. HTRI (Heat Transfer Research, Inc.) is a leading software suite used by engineers and designers to model, simulate, and analyze heat exchangers for diverse applications across industries. In this comprehensive guide, we will delve into the intricacies of modeling and simulating heat exchangers in HTRI, covering everything from basic concepts to advanced techniques for optimal performance and efficiency.
Section 1: Understanding Heat Exchangers
1.1 Overview of Heat Exchangers: Heat exchangers are devices designed to transfer heat from one fluid stream to another, either within a single phase or between multiple phases. They are essential components in thermal systems, HVAC systems, power plants, chemical processes, and refrigeration systems, enabling efficient heat transfer and energy utilization.
1.2 Types of Heat Exchangers: Heat exchangers come in various types and configurations, each suited to specific applications and operating conditions. Common types include shell-and-tube heat exchangers, plate heat exchangers, finned-tube heat exchangers, air-cooled heat exchangers, and double-pipe heat exchangers, each offering unique advantages in terms of heat transfer efficiency, pressure drop, and cost-effectiveness.
1.3 Importance of Heat Exchanger Analysis: Analyzing heat exchangers is essential for optimizing performance, maximizing energy efficiency, and ensuring safe and reliable operation. By modeling and simulating heat exchangers, engineers can evaluate thermal performance, predict operating conditions, and optimize design parameters to meet process requirements and regulatory standards.
Section 2: Introduction to HTRI Software
2.1 Overview of HTRI: HTRI is a comprehensive software suite developed by Heat Transfer Research, Inc. for the design, analysis, and optimization of heat exchangers. It provides engineers and designers with powerful tools for modeling heat exchanger geometries, simulating heat transfer processes, and predicting performance characteristics under various operating conditions.
2.2 HTRI Modules and Capabilities: HTRI software consists of modules tailored to specific aspects of heat exchanger analysis, including Xchanger Suite, Xist, Xhpe, Xvib, Xpfe, and Xfh. These modules offer capabilities for thermal design, mechanical design, vibration analysis, fouling analysis, pressure drop calculation, and performance prediction across a wide range of heat exchanger types and configurations.
2.3 Benefits of Using HTRI: HTRI software provides engineers and designers with several benefits, including accurate prediction of heat transfer rates, pressure drops, and temperature profiles in heat exchangers. It enables rapid design iteration, optimization of design parameters, and evaluation of alternative configurations to achieve optimal performance and efficiency.
Section 3: Modeling Heat Exchangers in HTRI
3.1 Geometry Definition: Engineers begin by defining the geometry of the heat exchanger within the HTRI software environment. They specify parameters such as shell diameter, tube length, tube diameter, baffle spacing, tube pitch, fin geometry, and flow arrangement to accurately represent the physical configuration of the heat exchanger.
3.2 Fluid Properties and Operating Conditions: Engineers input fluid properties and operating conditions for both the hot and cold fluid streams within the heat exchanger. They specify parameters such as fluid type, temperature, flow rate, pressure, viscosity, density, heat capacity, and thermal conductivity to model fluid behavior and heat transfer characteristics accurately.
3.3 Heat Transfer Mechanisms: HTRI allows engineers to model various heat transfer mechanisms, including conduction, convection, and radiation, within the heat exchanger. Engineers specify boundary conditions, heat transfer coefficients, fouling factors, and other parameters to accurately simulate heat transfer processes and predict thermal performance.
Section 4: Simulating Heat Exchanger Performance
4.1 Thermal Analysis: Engineers use HTRI software to perform thermal analysis of heat exchangers, predicting heat transfer rates, temperature profiles, and thermal efficiency under specified operating conditions. They analyze factors such as heat exchanger effectiveness, NTU (Number of Transfer Units), LMTD (Log Mean Temperature Difference), and UA (Overall Heat Transfer Coefficient) to evaluate thermal performance.
4.2 Pressure Drop Calculation: HTRI enables engineers to calculate pressure drops and flow distribution within heat exchangers, considering fluid velocities, friction factors, entrance and exit losses, and geometric constraints. Engineers analyze pressure drop profiles, pumping power requirements, and flow maldistribution to optimize heat exchanger design and minimize energy consumption.
4.3 Vibration Analysis: Engineers use HTRI software to perform vibration analysis of heat exchangers, predicting natural frequencies, mode shapes, and vibration amplitudes under specified operating conditions. They assess factors such as tube vibration, flow-induced vibration, and structural integrity to ensure safe and reliable operation of the heat exchanger.
Section 5: Advanced Techniques and Optimization Strategies
5.1 Heat Exchanger Design Optimization: HTRI supports design optimization techniques to improve the performance and efficiency of heat exchangers. Engineers leverage optimization algorithms, parametric studies, and sensitivity analyses to explore design alternatives, refine design parameters, and achieve optimal heat exchanger configurations.
5.2 Fouling Analysis and Mitigation: HTRI software includes capabilities for fouling analysis, enabling engineers to predict fouling rates, fouling resistance, and performance degradation over time. Engineers analyze factors such as fouling mechanisms, fouling mitigation strategies, and cleaning intervals to minimize fouling-related impacts on heat exchanger performance.
5.3 Retrofit and Revamp Studies: HTRI facilitates retrofit and revamp studies of existing heat exchangers to improve performance, extend service life, and meet changing process requirements. Engineers evaluate retrofit options, alternative materials, and design modifications to enhance heat exchanger efficiency, reliability, and maintainability.
Section 6: Best Practices and Tips
6.1 Accurate Modeling and Simulation: Ensure accurate modeling and simulation of heat exchangers by using validated correlations, empirical data, and experimental results for fluid properties, heat transfer coefficients, and pressure drop predictions. Calibrate simulation models against experimental data to validate accuracy and reliability of simulation results.
6.2 Sensitivity Analysis: Conduct sensitivity analysis to assess the impact of key design parameters and operating conditions on heat exchanger performance. Identify critical factors affecting thermal efficiency, pressure drop, and vibration characteristics to prioritize optimization efforts and design improvements.
6.3 Continuous Learning and Professional Development: Stay updated on the latest developments, advancements, and best practices in heat exchanger modeling and simulation. Participate in training programs, workshops, and technical conferences to enhance proficiency in HTRI software, heat transfer principles, and engineering methodologies.
Conclusion: Modeling and simulating heat exchangers in HTRI provides engineers and designers with powerful tools for optimizing thermal performance, maximizing energy efficiency, and ensuring reliable operation across a wide range of industrial applications. By mastering the fundamentals, methodologies, and advanced techniques discussed in this guide, engineers can leverage HTRI software to design innovative heat exchanger solutions, address complex engineering challenges, and achieve sustainable process improvements. With its comprehensive features, robust simulation capabilities, and intuitive user interface, HTRI continues to be a trusted tool in the field of heat transfer research and engineering, empowering users to push the boundaries of heat exchanger design and optimization.