Mastering Conveyor System Modeling and Simulation in FlexSim: A Comprehensive Guide
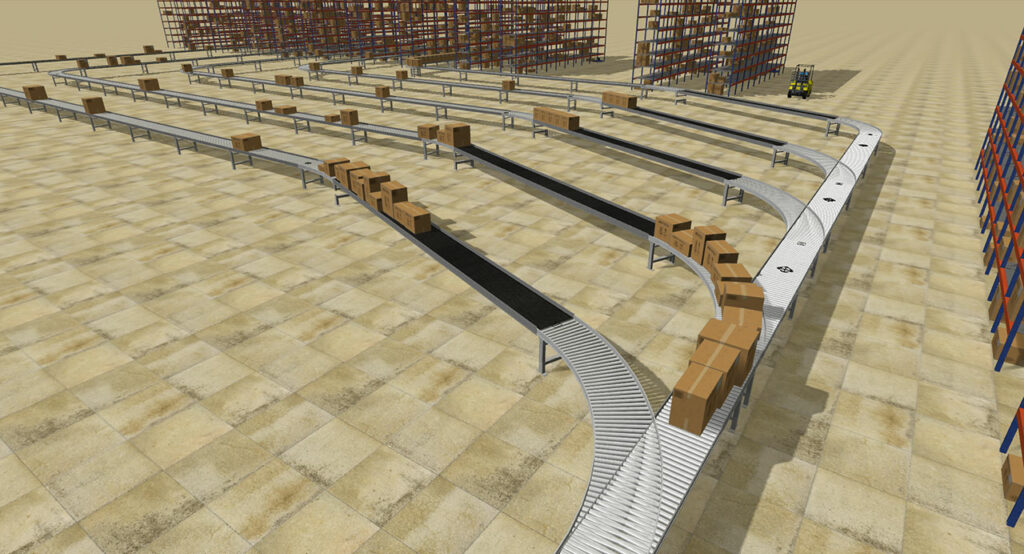
Introduction: Conveyor systems are ubiquitous in manufacturing, logistics, and material handling industries, facilitating the movement of goods, products, and materials throughout production facilities, warehouses, and distribution centers. Modeling and simulating conveyor systems are essential for optimizing throughput, minimizing bottlenecks, and improving operational efficiency. FlexSim is a powerful simulation software tool used by engineers and designers to model, simulate, and analyze conveyor systems in a virtual environment. In this comprehensive guide, we will explore the intricacies of modeling and simulating conveyor systems in FlexSim, covering everything from system design to performance analysis and optimization techniques.
Section 1: Understanding Conveyor Systems
1.1 Overview of Conveyor Systems: Conveyor systems are mechanical devices designed to transport goods, products, or materials from one location to another within a facility or along a predefined path. They consist of various components such as belts, rollers, pulleys, motors, sensors, and controls, which work together to move and control the flow of materials.
1.2 Types of Conveyor Systems: Conveyor systems come in a variety of configurations and types, each suited to specific applications and material handling requirements. Common types include belt conveyors, roller conveyors, chain conveyors, screw conveyors, and overhead conveyors, each offering unique advantages in terms of throughput, speed, and flexibility.
1.3 Importance of Simulation: Simulating conveyor systems is crucial for optimizing system design, layout, and operation, as well as for evaluating performance, identifying bottlenecks, and improving efficiency. By using simulation software like FlexSim, engineers can create virtual models of conveyor systems, conduct experiments, and analyze results to make informed decisions and implement improvements.
Section 2: Introduction to FlexSim Software
2.1 Overview of FlexSim: FlexSim is a comprehensive simulation software platform developed for modeling and analyzing complex systems, including conveyor systems, manufacturing processes, supply chains, and logistics operations. It provides engineers and designers with powerful tools for building virtual models, conducting experiments, and visualizing results in a 3D environment.
2.2 FlexSim Features and Capabilities: FlexSim offers a wide range of features and capabilities for modeling conveyor systems, including drag-and-drop model building, library of pre-built objects and components, customizable simulation logic, 3D visualization, animation, statistical analysis, and optimization algorithms for system performance improvement.
2.3 Benefits of Using FlexSim: FlexSim provides several benefits for engineers and designers involved in conveyor system simulation, including rapid model development, realistic visualization, dynamic animation, and comprehensive analysis tools. It enables users to simulate complex scenarios, test different configurations, and optimize system performance with confidence.
Section 3: Modeling Conveyor Systems in FlexSim
3.1 Model Building: Engineers begin by building a virtual model of the conveyor system within the FlexSim environment. They use drag-and-drop tools to create conveyor segments, define paths, specify conveyor components, and configure system parameters such as speed, capacity, and flow rates.
3.2 Component Configuration: FlexSim offers a library of pre-built conveyor components, including belts, rollers, motors, sensors, diverters, and controls, which engineers can customize to match the specifications of the real-world conveyor system. Engineers configure component properties, behaviors, and interactions to accurately represent system dynamics and operational characteristics.
3.3 System Layout and Integration: Engineers design the layout of the conveyor system within the FlexSim environment, taking into account factors such as material flow, process requirements, space constraints, and equipment placement. They integrate conveyor segments with other system components, such as workstations, storage areas, loading docks, and packaging stations, to simulate end-to-end material handling operations.
Section 4: Simulating Conveyor System Performance
4.1 Dynamic Simulation: FlexSim simulates the behavior of the conveyor system in real-time, capturing dynamic interactions, material flow, and system responses to changing conditions. Engineers run simulations to observe system behavior, analyze performance metrics, and identify bottlenecks, congestion points, and inefficiencies in material handling operations.
4.2 Throughput Analysis: Engineers use FlexSim to analyze throughput, cycle times, and material flow rates within the conveyor system. They collect performance data, generate statistical reports, and visualize key metrics such as throughput, utilization, queue lengths, and dwell times to assess system efficiency and identify areas for improvement.
4.3 Resource Utilization: FlexSim enables engineers to analyze resource utilization and capacity constraints within the conveyor system, including equipment utilization, manpower requirements, and material handling efficiency. Engineers identify resource bottlenecks, analyze resource allocation, and optimize resource utilization to improve system productivity and throughput.
Section 5: Advanced Techniques and Optimization Strategies
5.1 Experimentation and Scenario Analysis: Engineers conduct experimentation and scenario analysis in FlexSim to explore different configurations, operational strategies, and system parameters. They simulate alternative scenarios, adjust simulation inputs, and analyze outcomes to evaluate performance trade-offs and identify optimal design solutions for the conveyor system.
5.2 Optimization Algorithms: FlexSim offers optimization algorithms and tools for improving system performance and efficiency. Engineers use optimization techniques such as genetic algorithms, simulation-based optimization, and parameter tuning to identify optimal configurations, scheduling policies, and control strategies for the conveyor system.
5.3 Integration with Control Systems: FlexSim supports integration with control systems, PLCs (Programmable Logic Controllers), and SCADA (Supervisory Control and Data Acquisition) systems for real-time control and monitoring of the conveyor system. Engineers develop control logic, implement automation routines, and interface with external control systems to simulate closed-loop control and feedback mechanisms.
Section 6: Best Practices and Tips for Conveyor System Simulation
6.1 Validation and Verification: Validate FlexSim models against real-world data, observations, and measurements to ensure accuracy and reliability of simulation results. Compare simulated performance with empirical data, conduct sensitivity analyses, and verify model assumptions to build confidence in simulation outcomes and decision-making.
6.2 Model Abstraction and Simplification: Simplify complex conveyor system models by abstracting unnecessary details, focusing on key components, and using simplified representations where appropriate. Balance model fidelity with computational efficiency to achieve accurate results without compromising simulation performance and scalability.
6.3 Continuous Improvement and Iteration: Adopt a continuous improvement approach to conveyor system simulation, iterating on model designs, experimenting with different configurations, and incorporating feedback from stakeholders. Use simulation results to drive decision-making, implement improvements, and optimize system performance over time.
Conclusion: Modeling and simulating conveyor systems in FlexSim provide engineers and designers with a powerful tool for optimizing material handling operations, improving throughput, and enhancing operational efficiency. By mastering the principles, techniques, and best practices discussed in this guide, engineers can leverage FlexSim to design innovative conveyor systems, analyze performance trade-offs, and implement improvements with confidence. With its intuitive interface, advanced simulation capabilities, and comprehensive analysis tools, FlexSim continues to be a trusted platform for modeling and simulating complex systems in manufacturing, logistics, and material handling industries, empowering users to make data-driven decisions and achieve operational excellence.