How to Perform Fatigue Analysis in ANSYS
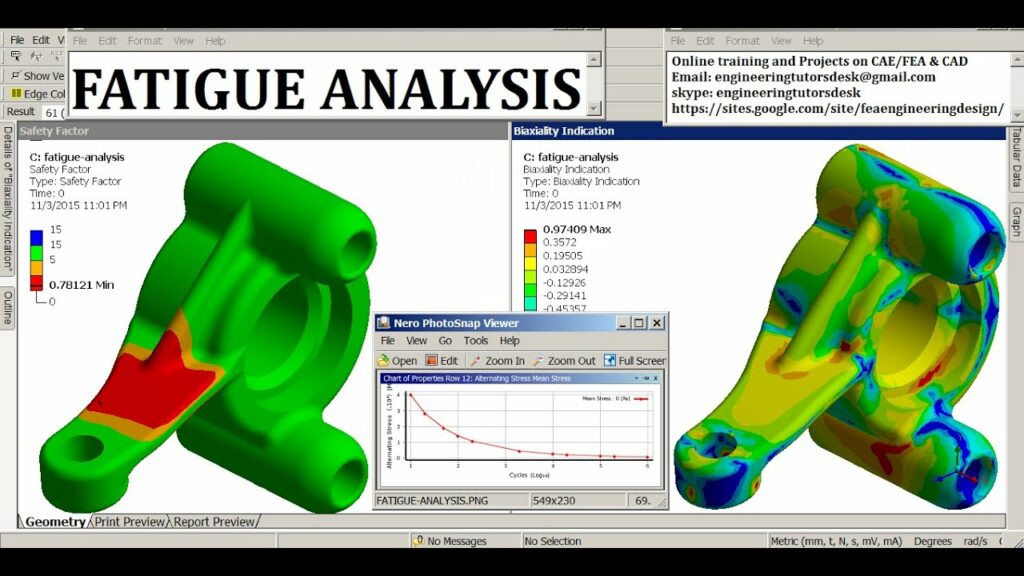
Performing fatigue analysis in ANSYS involves assessing the durability and lifespan of mechanical components subjected to cyclic loading conditions. Fatigue analysis is crucial in engineering design to predict potential failures due to repeated stresses over time, which are common in applications ranging from aerospace structures and automotive components to machinery and consumer products. ANSYS provides powerful tools and methodologies to simulate fatigue behavior accurately, integrating advanced fatigue life prediction techniques with finite element analysis (FEA). This comprehensive guide will cover the theory, setup procedures, analysis types, interpretation of results, and best practices for performing fatigue analysis in ANSYS.
Table of Contents
- Introduction to Fatigue Analysis in ANSYS
- Fundamentals of Fatigue Failure
- Preparing Geometry and Mesh for Fatigue Analysis
- Defining Material Properties and Loading Conditions
- Setting Up Fatigue Analysis in ANSYS
- Types of Fatigue Analysis
- Post-Processing and Interpreting Results
- Advanced Techniques in Fatigue Analysis
- Best Practices for Fatigue Analysis
- Conclusion
1. Introduction to Fatigue Analysis in ANSYS
Fatigue analysis evaluates the structural integrity of components subjected to cyclic loading, which can lead to failure over time even if stresses are below the material’s yield strength. ANSYS offers sophisticated tools to simulate fatigue phenomena accurately, aiding engineers in designing robust and reliable products that withstand long-term operational conditions.
2. Fundamentals of Fatigue Failure
Fatigue failure occurs due to cyclic loading, causing progressive damage and eventual fracture of a material. Key concepts include:
- S-N Curve: Represents the relationship between stress amplitude (S) and number of cycles to failure (N).
- Fatigue Life: Predicts the number of cycles a material can endure before failure.
- Loading Conditions: Include tension-compression, bending, torsion, and combinations thereof.
3. Preparing Geometry and Mesh for Fatigue Analysis
- Geometry Import: Import CAD geometry into ANSYS Workbench or Mechanical.
- Geometry Cleanup: Ensure geometry is clean and suitable for meshing.
- Mesh Generation: Create a finite element mesh using ANSYS Meshing or TGrid.
- Mesh Refinement: Refine mesh in critical areas to capture stress concentrations and load paths accurately.
4. Defining Material Properties and Loading Conditions
- Material Assignment: Define material properties such as yield strength, elastic modulus, and fatigue properties (S-N curve parameters).
- Loading Definition: Specify loading conditions including magnitudes, frequencies, and types (static, dynamic, cyclic).
- Boundary Conditions: Apply constraints and boundary conditions relevant to the fatigue analysis scenario.
5. Setting Up Fatigue Analysis in ANSYS
- Module Selection: Choose the appropriate fatigue analysis module in ANSYS Workbench (e.g., Fatigue Module).
- Fatigue Life Calculation: Configure analysis settings for fatigue life prediction based on selected criteria (e.g., stress-life, strain-life).
- Solver Setup: Define solver settings, convergence criteria, and solution controls.
6. Types of Fatigue Analysis
- Stress-Life (S-N) Approach: Predicts fatigue life based on stress amplitudes using empirical S-N curve data.
- Strain-Life Approach: Estimates fatigue life considering local material strains and cyclic stress-strain behavior.
- Critical Plane Analysis: Identifies critical planes where fatigue damage accumulates most rapidly.
7. Post-Processing and Interpreting Results
- Fatigue Life Prediction: Obtain fatigue life estimates for components under specified loading conditions.
- Damage Accumulation: Visualize and analyze fatigue damage distribution across the structure.
- Visualization Tools: Utilize contour plots, histograms, and fatigue damage spectrum (Rainflow counting) for result interpretation.
8. Advanced Techniques in Fatigue Analysis
- Variable Amplitude Loading: Simulate real-world loading profiles with varying amplitudes and frequencies.
- Multiaxial Fatigue: Analyze fatigue behavior under combined loading conditions (tension-compression, bending-torsion).
- Probabilistic Fatigue Analysis: Incorporate uncertainties in material properties and loading conditions for reliability assessment.
9. Best Practices for Fatigue Analysis
- Validation: Validate simulation results against experimental data or known standards.
- Mesh Sensitivity: Perform mesh sensitivity studies to ensure accurate stress prediction and fatigue life estimation.
- Iterative Design Improvement: Iteratively refine designs based on fatigue analysis results to enhance durability and reliability.
10. Conclusion
Fatigue analysis in ANSYS is essential for predicting and mitigating potential failures in mechanical components subjected to cyclic loading. By following the steps outlined in this guide and leveraging ANSYS’s advanced simulation capabilities, engineers can optimize designs, improve product reliability, and ensure structural integrity over extended operational lifetimes. Understanding fatigue phenomena, selecting appropriate analysis methods, and applying best practices empower engineers to design safer, more durable products across various industries. ANSYS’s comprehensive fatigue analysis tools support innovation and engineering excellence, enabling the development of high-performance components that meet stringent durability requirements and exceed customer expectations.