How to Conduct Optimization Studies in ANSYS
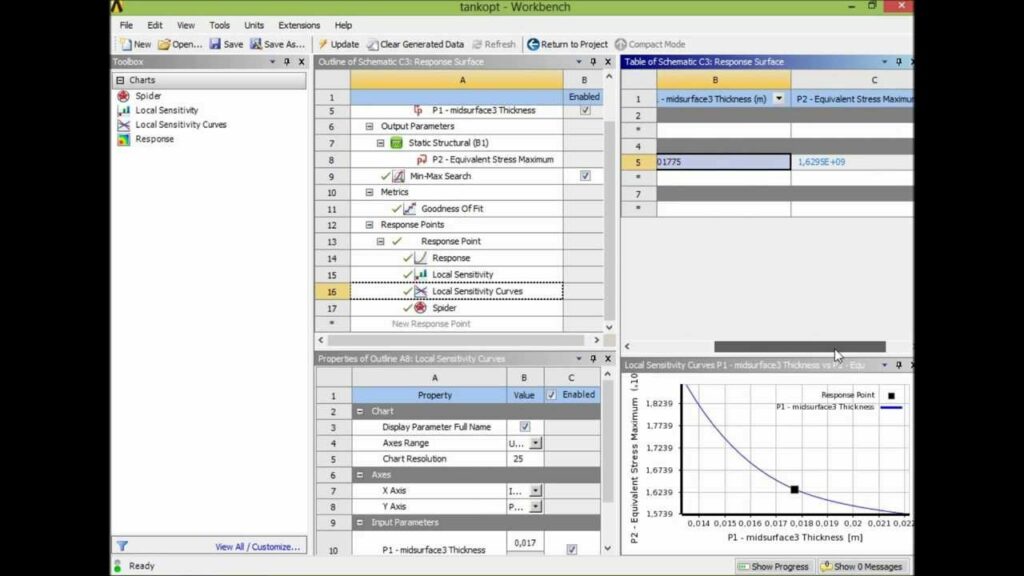
Conducting optimization studies in ANSYS involves utilizing advanced computational techniques to systematically improve and optimize engineering designs. Optimization in ANSYS encompasses a wide range of methodologies and tools that allow engineers to explore design variations, minimize costs, maximize performance metrics, and meet specified objectives. This comprehensive guide will cover the theory, setup procedures, types of optimization studies, optimization algorithms, interpretation of results, best practices, and applications of optimization in ANSYS.
Table of Contents
- Introduction to Optimization Studies in ANSYS
- Fundamentals of Optimization
- Setting Up for Optimization Studies
- Types of Optimization Studies
- Optimization Algorithms in ANSYS
- Interpreting Optimization Results
- Advanced Techniques in Optimization
- Best Practices for Optimization Studies
- Applications of Optimization in ANSYS
- Conclusion
1. Introduction to Optimization Studies in ANSYS
Optimization studies in ANSYS involve leveraging computational tools to enhance engineering designs by iteratively refining parameters and variables to achieve optimal solutions. These studies are critical for improving performance metrics, reducing material usage, and meeting design constraints across various industries such as aerospace, automotive, biomedical, and consumer goods.
2. Fundamentals of Optimization
- Objective Functions: Define metrics to optimize (e.g., minimize stress, maximize stiffness, minimize weight).
- Design Variables: Identify parameters that can be adjusted (e.g., dimensions, material properties, boundary conditions).
- Constraints: Specify limitations or requirements (e.g., maximum stress, manufacturing constraints, performance targets).
3. Setting Up for Optimization Studies
- Simulation Setup: Establish the baseline simulation model in ANSYS Workbench or ANSYS Mechanical.
- Parameterization: Define design variables and their ranges or constraints for optimization.
- Objective Definition: Specify the objective function to optimize (e.g., minimize mass, maximize natural frequency).
4. Types of Optimization Studies
- Single-Objective Optimization: Focus on optimizing one objective function (e.g., minimize weight).
- Multi-Objective Optimization: Optimize conflicting objectives simultaneously (e.g., minimize weight while maximizing stiffness).
- Design Space Exploration: Explore multiple design configurations to identify trade-offs and optimal solutions.
5. Optimization Algorithms in ANSYS
- Gradient-Based Algorithms: Utilize gradient information for efficient convergence (e.g., Gradient Descent, Sequential Quadratic Programming).
- Direct Search Methods: Explore design space without gradient information (e.g., Genetic Algorithms, Particle Swarm Optimization).
- Response Surface Methods: Approximate complex objective functions with simpler surrogate models (e.g., Design of Experiments, Polynomial Regression).
6. Interpreting Optimization Results
- Optimal Solution: Identify the set of design variables that yield the best objective function value.
- Sensitivity Analysis: Analyze the impact of design variables on the objective function and constraints.
- Trade-off Analysis: Evaluate trade-offs between conflicting objectives and constraints.
7. Advanced Techniques in Optimization
- Topology Optimization: Redesign structures by distributing material optimally within a predefined design space to achieve desired performance metrics.
- Probabilistic Optimization: Incorporate uncertainties in input parameters (e.g., material properties, loading conditions) for robust design optimization.
- Multi-disciplinary Optimization (MDO): Integrate multiple disciplines (e.g., structural, thermal, fluid dynamics) to optimize designs across interconnected domains.
8. Best Practices for Optimization Studies
- Clear Objectives: Define clear and measurable objectives for optimization to guide the study effectively.
- Iterative Refinement: Iteratively refine design variables based on optimization results to converge towards optimal solutions.
- Verification and Validation: Validate optimized designs through simulations, experimental testing, or comparison with benchmarks.
9. Applications of Optimization in ANSYS
Optimization in ANSYS finds extensive applications in various industries and engineering disciplines:
- Aerospace: Optimize aircraft structures for weight reduction while maintaining structural integrity.
- Automotive: Enhance vehicle performance by optimizing engine components, chassis design, and aerodynamics.
- Biomedical: Improve medical devices by optimizing materials, geometries, and performance characteristics.
- Consumer Goods: Optimize product designs for durability, usability, and cost-effectiveness.
10. Conclusion
Optimization studies in ANSYS empower engineers and researchers to innovate, improve efficiency, and achieve design excellence across diverse engineering applications. By leveraging advanced computational tools, optimization algorithms, and best practices outlined in this guide, engineers can systematically explore design alternatives, enhance product performance, and meet stringent design requirements. ANSYS’s robust optimization capabilities support iterative design refinement, enabling the development of optimal solutions that balance performance metrics, constraints, and objectives effectively. Mastering optimization techniques in ANSYS contributes to advancing technology, improving competitiveness, and delivering high-quality, optimized designs that address complex engineering challenges with precision and reliability.